Technology
Technical Description
SG 50
SG 75
SG 100
SG 200
SG 300
SG 400
SG 500
1. Technology
The INTEC Synthesis Gas Systems generate electrical energy to be fed-in to the public grid or to other industrial plants by thermal recovery of organic residues from waste of commerce and industry, health sector, agriculture and forestry, municipalities and other sectors (except toxic and hazardous residues). Main plant components of the plant system are:- Plant unit for waste sorting and conditioning (INTEC WS Series)
- Plant unit for the generation of synthesis gas (INTEC SG Series)
- Plant unit for the generation of electrical energy (INTEC PP Series)
- Steam Turbine Plant for the heat utilisation from the generators for the generation of additional electrical power
- Separation, conditioning and drying of the delivered waste.
- Generation of synthesis gas from conditioned waste with the patented INTEC Thermolytic Cracking Process (INTEC-TCP®).
- Combustion of the synthesis gas in gas Otto-engines as generator drives for electricity generation and waste heat recovery for power production with a Steam Turbine Plant.
1.A Operation Mode of the Waste Treatment Plant (INTEC WS Series)
The drawing layout shows various possibilities for the processing of the waste. In the following, the method is first described, in which the drying of the waste is mainly carried out using exhaust heat from synthesis gas production and electricity generation. In this case, the possible evaporation quantity and thus the degree of moisture of the refuse are limited since the supply of additional energy is to be avoided as far as possible. If the amount of waste is greater than or equal to 30%, biological drying is required. Whether only one or a combination of the two methods is used depends on the properties of the garbage which has to be processed. The design parameters for the plant are determined by the garbage properties, the intended use of the final product and the size of the synthesis gas plant. The garbage is delivered by truck. The mass of the material delivered is collected via a vehicle balance before it is unloaded into the acceptance bunker. The acceptance bunker is located in a closed processing hall. Air sluices at the tipping points ensure that no unwanted odors escape. The suctioned air then passes through the cleaning system. The floor of the acceptance bunker consists of slotted concrete slabs, through which the leaking seepage can flow to the treatment system. From here, the coarse crusher, which is protected by a bar strainer before oversize the waste components, is fed by means of a bunker crane.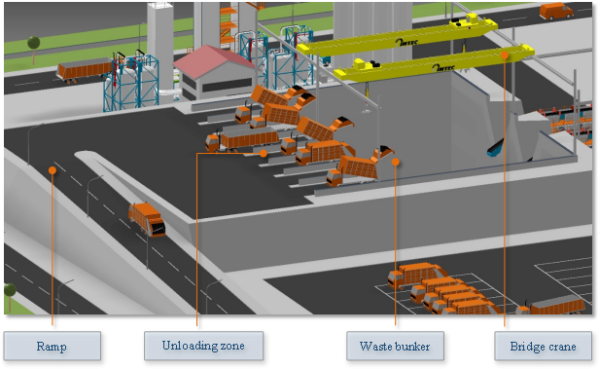
Illustration 1: Unloading zone and acceptance bunker
The subsequently following sieving units separate the material stream in a coarse and fine fraction. With a system of belt conveyors, the fine fraction is directly transported to the separators for ferrous and non-ferrous metals, glass and minerals to be discharged. The accordingly conditioned material stream is subsequently conveyed to a drying unit, where by means of heated air (residual heat from the gas- and electricity- generation) with a temperature of approx. 70 – 80 °C, the necessary residual moisture of approx. 10 – 15 % is achieved. The coarse fraction is conveyed to the fine shredders and subsequently transported to the separate sorting lines. Analogous to the procedure with the fine fraction, the discharge of inorganic material and pre-drying is carried out. The material streams from the dryers of one line are collected and conveyed to the respectively designated sieving unit. The fraction with a grain size < 35 mm serves as the input material for the reactors whilst the oversized material is re-fed to the fine shredding unit.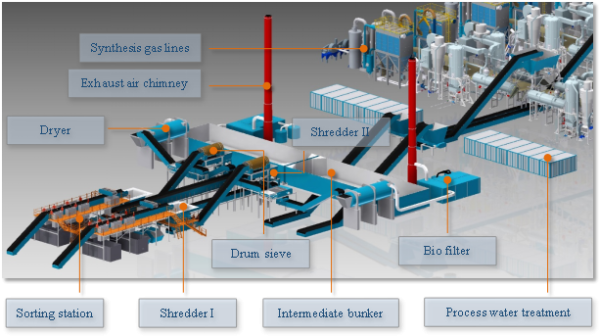
Illustration 2: Waste conditioning
For a moisture content of more than 30%, INTEC recommends the use of a mechanical-biological treatment plant for economic reasons. The system offered by INTEC, as shown in the layout as item no. 17 contains all necessary premises and equipment for continuous plant operation (see also separate MBT description).1.B Operation Mode of the Synthesis Gas Plant Units (INTEC SG Series)
The synthesis gas process serves the chemical and energetic conversion of substitute fuels and biomass into a synthesis gas in several process steps. The produced synthesis gas with an average calorific value of 25,000 kJ / m³ can be used both for electricity generation in gas engines and turbines as well as for the production of process heat. A synthesis gas plant is a modular system consisting of one or more basic lines corresponding to the selected size. The main components of a base line are: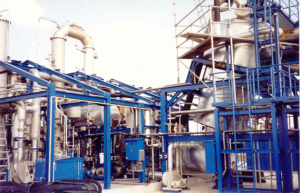
- Main Reactor
- Secondary reactor
- Crack reactors
- Scrubber
- Attendant facilities
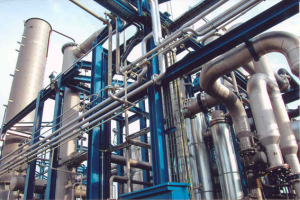
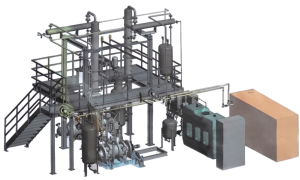
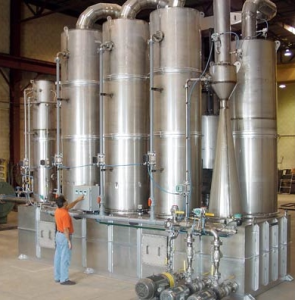
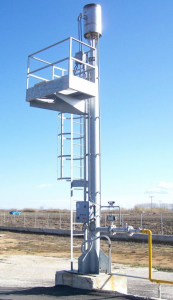
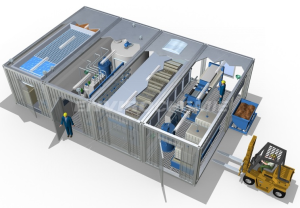
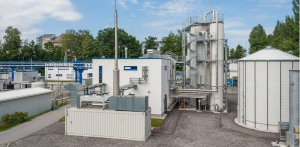
1.C Mode of the Power Generation Plant Units Operation
A gas engine system and waste heat recovery with steam turbine systems are used for generating electricity. The synthesis gas, buffered in intermediary storage tanks, reaches the gas Otto-engines coupled with 10 kV generators via a compressor system. In case of identical voltage, the generated electrical energy can be directly fed-in to the medium-voltage grid. In case of differing values, the voltage is transformed to the required value – if necessary, also to the high-voltage grid up to 110 kV. The exhaust gas stream of the gas Otto-engines is led through the primary circuit of a waste heat steam boiler (heat exchanger). The energy contained therein evaporates the working medium (water) in the secondary circuit of the waste heat steam boiler. The steam drives the steam turbine connected to a generator of the post-generation plant (steam turbine system). The electricity generated here is available to the consumers or the grid feed-in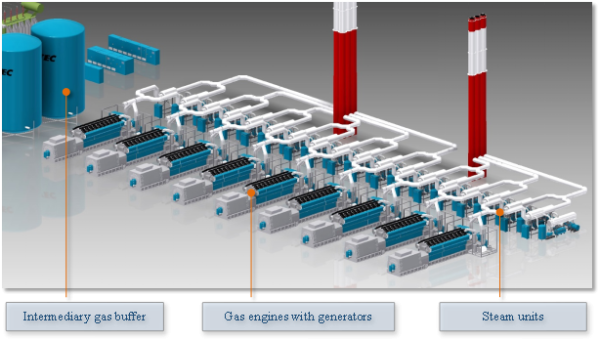
Illustration 3: Power generation from synthesis gas
2. Process Features
|
|
||||
|
|
Table 1: Process features
3. Utilisable Input Materials
|
|
|
Table 2: Utilisable input materials
4. Plant Data
4.A Quantities per Production Line
- Reactor throughput: up to 3,3 t/h conditioned organic waste(including 10 m% residual moisture)
- Producible gas volume: 1,600 – 2,400 Nm³/h
- Energy amount (electrical)approx. 1.2 to 1.8 MWh/t conditioned waste
5. Concluding Remarks
The synthesis gas generation and utilisation is a multi-staged process and bases on the partial steps drying, de-gassing, gasification, gas scrubbing, gas combustion and electricity generation. The application of the technology on the basis of the INTEC Thermolytic Cracking Process (INTEC-TCP®) allows a highly efficient utilisation of organic wastes for the generation of clean energy. The control of the complete system is carried out by a process control system (Siemens PCS 7), designed for automated operation including remote maintenance. This ensures the operational liability 24 hours, 7 days a week on 365 days a year. Important sensors and actuators are redundantly designed. For essential plant components, the power supply is secured by an uninterruptible power supply (UPS) and an emergency power supply.6. Patents
The technology, reactor and gasifier are secured by patents. The first patent was granted in December 2015.- Synthetic Gas Lines: 2
- Assumed moisture content of the waste: 50%
- Approximate Input Waste per day (Gross Waste): 260 tons
- Approximate Input Waste per year (Gross Waste): 83,600 tons
- Assumed energy content of the waste passing through the gasification lines: at least 20 MJ/kg
- Approximate Production of electricity per hour: 9 MW
- Synthetic Gas Lines: 3
- Assumed moisture content of the waste: 50%
- Approximate Input Waste per day (Gross Waste): 400 tons
- Approximate Input Waste per year (Gross Waste): 139,000 tons
- Assumed energy content of the waste passing through the gasification lines: at least 20 MJ/kg
- Approximate Production of electricity per hour: 13 MW
- Synthetic Gas Lines: 4
- Assumed moisture content of the waste: 50%
- Approximate Input Waste per day (Gross Waste): 530 tons
- Approximate Input Waste per year (Gross Waste): 188,000 tons
- Assumed energy content of the waste passing through the gasification lines: at least 20 MJ/kg
- Approximate Production of electricity per hour: 17 MW
- Synthetic Gas Lines: 8
- Assumed moisture content of the waste: 50%
- Approximate Input Waste per day (Gross Waste): 1,050 tons
- Approximate Input Waste per year (Gross Waste): 378,000 tons
- Assumed energy content of the waste passing through the gasification lines: at least 20 MJ/kg
- Approximate Production of electricity per hour: 44 MW
- Synthetic Gas Lines: 12
- Assumed moisture content of the waste: 50%
- Approximate Input Waste per day (Gross Waste): 1,600 tons
- Approximate Input Waste per year (Gross Waste): 567,000 tons
- Assumed energy content of the waste passing through the gasification lines: at least 20 MJ/kg
- Approximate Production of electricity per hour: 68 MW
- Synthetic Gas Lines: 16
- Assumed moisture content of the waste: 50%
- Approximate Input Waste per day (Gross Waste): 2,150 tons
- Approximate Input Waste per year (Gross Waste): 756,000 tons
- Assumed energy content of the waste passing through the gasification lines: at least 20 MJ/kg
- Approximate Production of electricity per hour: 93 MW
- Synthetic Gas Lines: 20
- Assumed moisture content of the waste: 50%
- Approximate Input Waste per day (Gross Waste): 2,650 tons
- Approximate Input Waste per year (Gross Waste): 946,000 tons
- Assumed energy content of the waste passing through the gasification lines: at least 20 MJ/kg
- Approximate Production of electricity per hour: 116 MW